Hydrogen embrittlement in civil engineering
Hydrogen embrittlement in civil engineering: An Underestimated Challenge for Fasteners and Connectors
In the world of construction, materials determine not only the quality and longevity of structures, but also their safety and reliability. Consequently, the selection and use of materials plays a crucial role in the design and construction of all types of buildings. A particularly important aspect is the chemical and physical integrity of the materials used. This is particularly important for connecting and fastening devices such as screws, bolts and anchors, which are essential components that hold structures together and must ensure their stability under a wide range of loads and environmental conditions, so it is crucial to pay attention to their performance. One process that can seriously affect the performance of fasteners is hydrogen embrittlement.
Hydrogen embrittlement is a phenomenon that can cause extensive damage to high strength fasteners. When metals, particularly high strength steels and alloys, are exposed to hydrogen atoms, they can lose their ductility (malleability) and become brittle. Hydrogen embrittlement is therefore a particularly serious problem in areas where high strength and reliability of the materials used are essential, underlining its critical importance in the construction industry. The phenomenon not only affects the performance of the fasteners, but also has a significant impact on the service life of the entire structure. It is therefore essential to proactively prevent material failure to ensure the long-term stability and safety of the structure.
Causes of Hydrogen Embrittlement
In order to understand and proactively manage the risk of possible hydrogen embrittlement, it is important to understand the basic conditions and causes under which the phenomenon occurs. On this basis, it is possible to select fasteners with the appropriate material and to take appropriate preventative and treatment measures. Hydrogen embrittlement can occur in a material when the following three conditions are present. The presence of hydrogen, the use of a susceptible material and the presence of stress.
Presence of hydrogen: For hydrogen to penetrate the material, it must first be present in sufficient quantities. Hydrogen can come from a variety of sources including manufacturing processes, corrosion reactions or environmental conditions. Hydrogen can be introduced during the manufacture or processing of the fastener, for example, by penetrating the metal during welding, galvanizing or etching. In addition, chemical or electrochemical corrosion can occur, particularly in acidic environments, where hydrogen ions are released and absorbed by the metal. Finally, hydrogen can enter the metal due to environmental conditions such as high pressure or high temperature, especially in the presence of hydrogen gas.
Susceptibility of a material: The susceptibility of a material to hydrogen embrittlement depends on a number of specific properties and conditions, so not all materials are equally susceptible to this type of embrittlement. Certain metals and alloys are more susceptible than others. Key factors include material composition and microstructure, strength and hardness, processing and heat treatment, and surface condition. For example, high strength metals are more susceptible than other materials due to the factors mentioned above. Their microstructure and strength means that they absorb and bind hydrogen atoms more easily, increasing the risk of cracking and fracture. Overall, the susceptibility of the material to hydrogen embrittlement is the result of a complex interaction of various physical and chemical properties. These factors must be taken into account when selecting and processing materials to minimize the risk of embrittlement.
Stress: External loads as well as internal stresses, which can result from manufacturing processes such as forging, rolling or welding, and contribute significantly to the risk of hydrogen embrittlement. Stress allows the hydrogen atoms to reach the critical areas in the metal, e.g. microcracks or defects, and trigger embrittlement there.
If the three conditions mentioned here are present at the same time, the risk of hydrogen embrittlement is significantly increased.
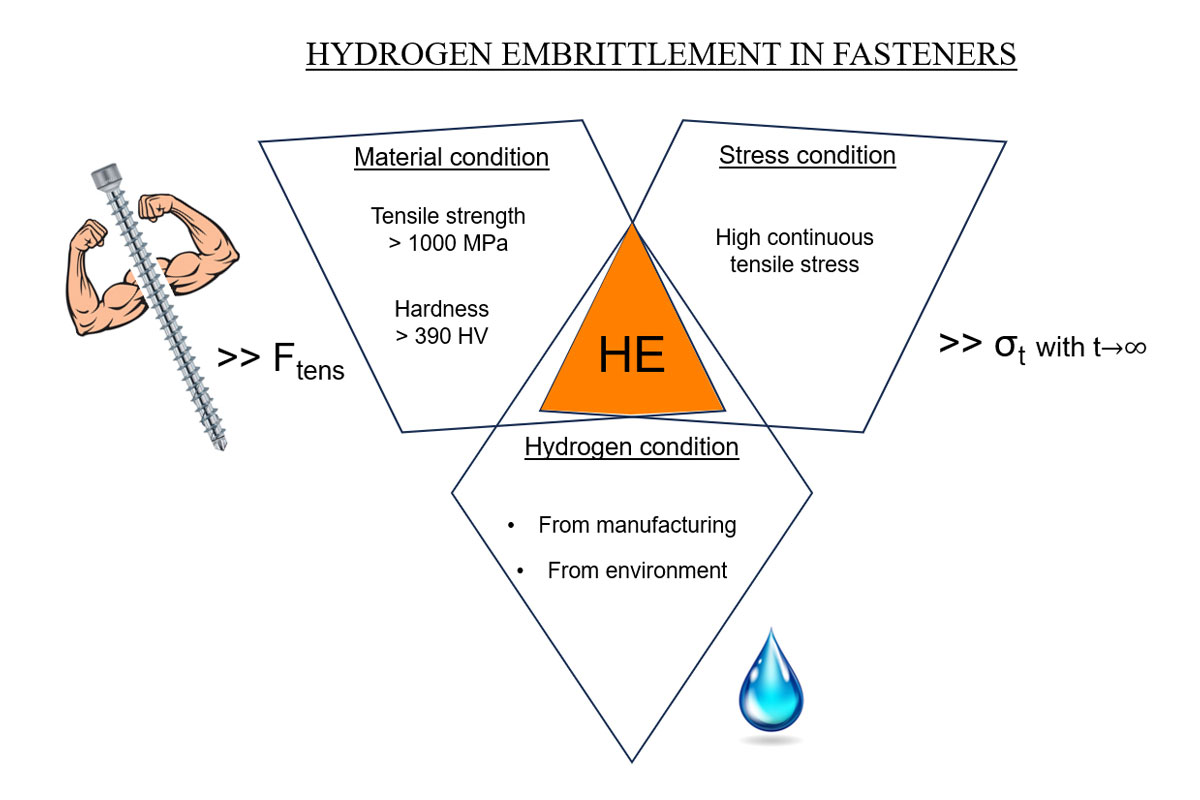
From penetration to fracture: How hydrogen embrittles metals
Hydrogen embrittlement is a serious threat to the safety and reliability of fasteners and connectors. The phenomenon can affect the mechanical properties of the metal, leading to unexpected material failure. This is particularly important in structural applications, where the presence of hydrogen in high strength steels and other susceptible alloys can lead to brittle fracture.
The process of hydrogen embrittlement usually takes place in 3 steps:
- Hydrogen absorption: During various manufacturing processes, such as acid cleaning or electroplating, corrosion processes or direct contact with hydrogen gas can cause carbon steel alloys to absorb hydrogen. The absorption is enhanced by the surface structure of the metal and can be influenced by external factors such as acidic environments or cathodic corrosion. In this first phase, hydrogen penetrates into the material.
- Diffusion: After hydrogen absorption has taken place, the hydrogen atoms move (diffuse) within the metal structure. Typically, the atoms tend to concentrate in areas of increased stress, such as cracks, inclusions, along grain boundaries or in areas of mechanical stress. Such accumulation ultimately leads to a change in material properties, increasing the risk of embrittlement and cracking or fracture within the material.
- Embrittlement: When hydrogen accumulates in certain areas of the metal and causes embrittlement. As hydrogen can weaken the metallic bonds, the material loses ductility and toughness, causing cracks to form and propagate under mechanical stress. This change can lead to brittle fracture under loads – even if these are lower than expected – and thus to failure of the fastener.

1. Hydrogen absorption
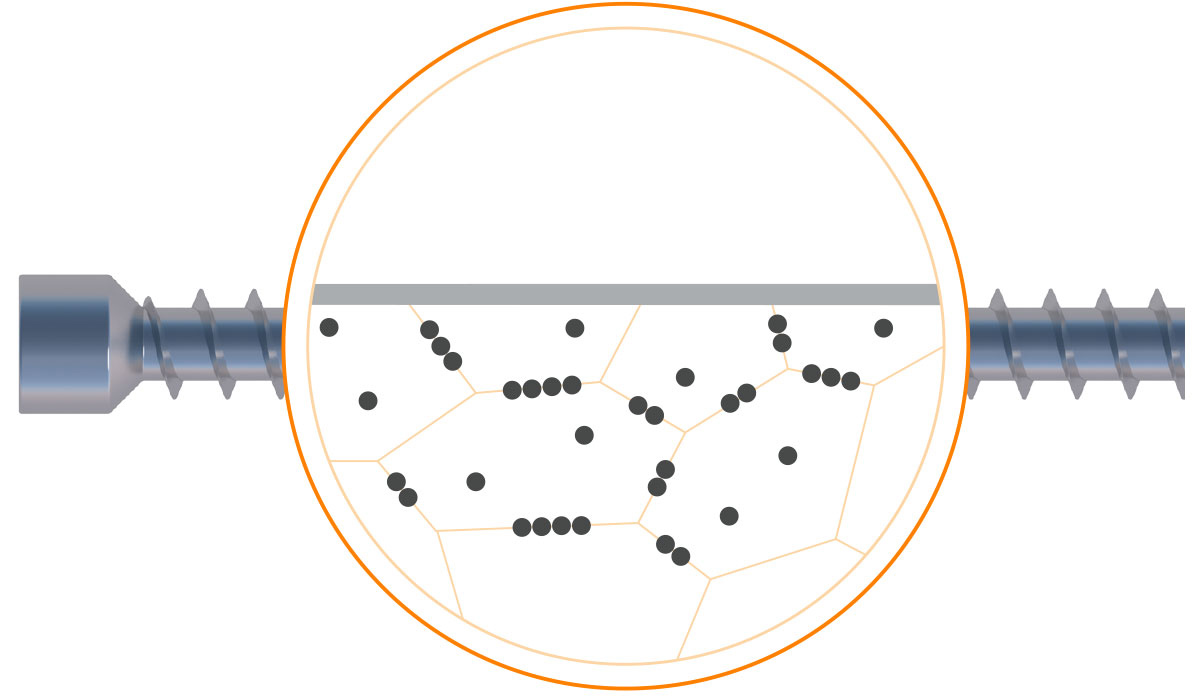
2. Hydrogen in preferential sties like grain boundaries, dislocations or impurities
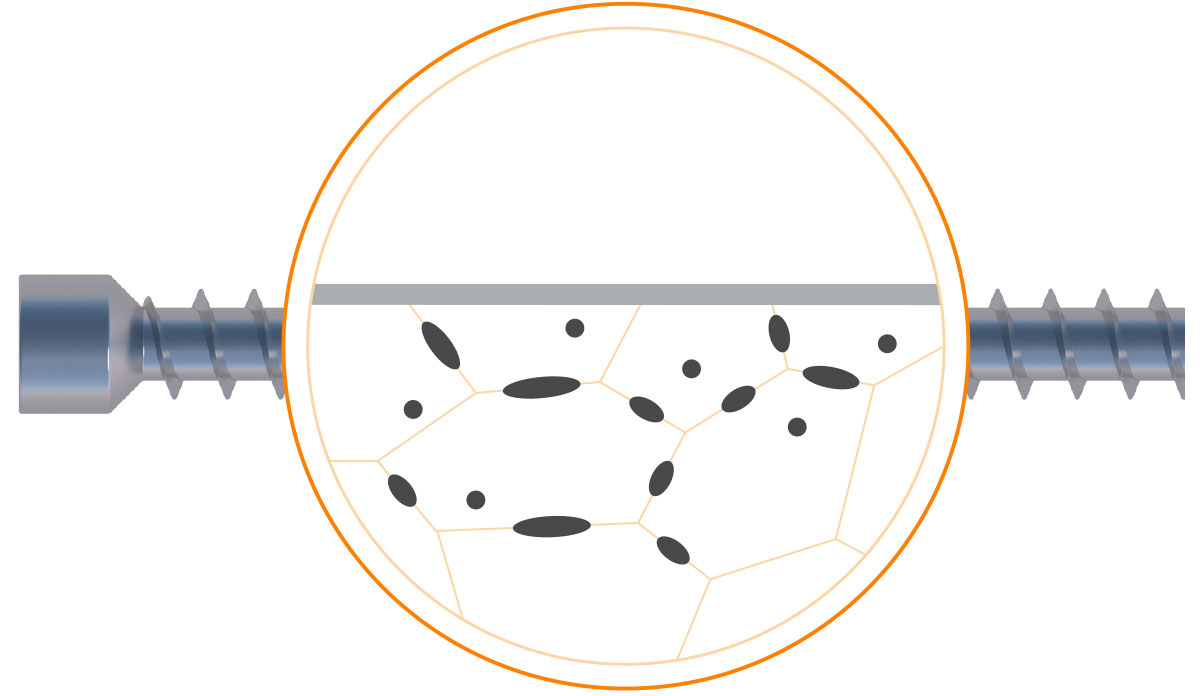
3. Attacks growth and leads to cracking under stress
Tempering to prevent hydrogen embrittlement of bolts
Hydrogen embrittlement is a phenomenon that can affect high strength fasteners. It is the permanent reduction in the ductility of steel due to absorbed hydrogen, leading to microcracking and eventual brittle failure. Heat treatment is critical in the manufacturing process of screws and other fasteners. It helps to achieve the required mechanical and material properties and to ensure the longevity of the products. One specific heat treatment technique is quenching and tempering. It is used to optimize the strength and hardness of the screw and to reduce the risk of hydrogen embrittlement. As a process, tempering is therefore a crucial step in the quality control of screw production.
Tempering is generally a heat treatment process in which a material is heated for an extended period of time – up to 24 hours. This is usually done before galvanizing and after hardening of the bolt, and involves heating the material to a temperature of 190 °C to 230 °C. This allows as much hydrogen as possible to be removed by casting and the remaining hydrogen to be trapped and immobilized in the steel structure. The aim of tempering is to reduce the stresses created in the metal by drawing and hardening during the manufacturing process, and to improve its toughness without significantly reducing its hardness. In addition, this heat treatment process helps to modify the microstructure of the screw so that it is less susceptible to the damaging effects of hydrogen.
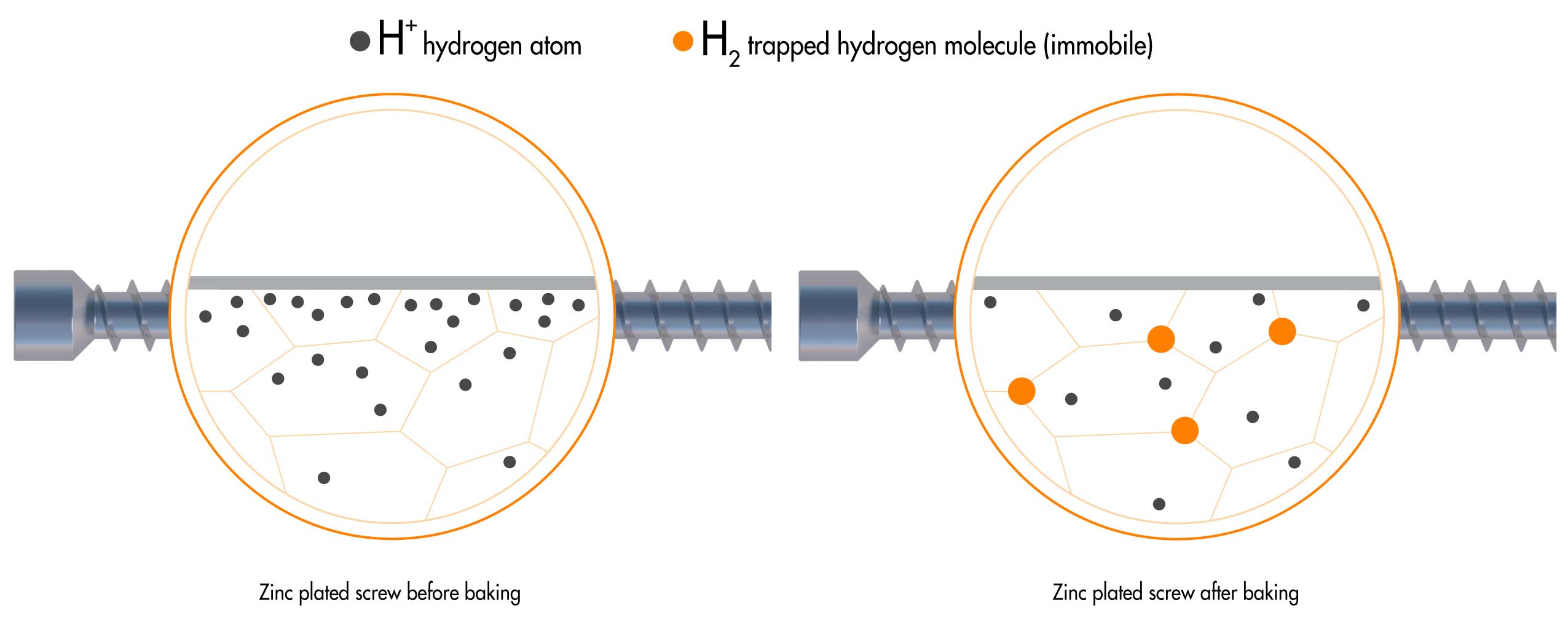
How Eurotec minimizes the risk of hydrogen embrittlement in screws and other fasteners
As a fastener specialist with 25 years' experience and our own manufacturing facility, we take a number of measures to limit the risk of hydrogen embrittlement. We rely on innovative manufacturing processes using the latest technology to meet our customers' requirements. As a manufacturer, we also place great emphasis on in-house production control, continuous process optimization and compliance with DIN EN ISO 9001 quality requirements. Eurotec's production facility covers an area of approximately 4,000 square metres, supplemented by additional external storage space, making us an efficient company.
One of Eurotec's main focuses is the in-house production of screws. Our quality-tested and patented screw solutions are used to build complex timber structures all over the world. The longevity and reliability of our screws is of paramount importance to us. Particular attention is paid to minimizing the risk of hydrogen embrittlement. Through careful material selection, precise manufacturing techniques and comprehensive quality control, we ensure that our screws can withstand even the most demanding conditions. Specifically, through a two-stage tempering process – before galvanizing and after hardening of the screws – we seek to reduce internal stresses in the metal and modify the microstructure to minimize hydrogen diffusion. In this way, we aim to significantly reduce the risk of hydrogen embrittlement and increase the safety and reliability of our products.
Note: Despite our intensive efforts, the occurrence of hydrogen embrittlement under exceptional conditions can never be completely eliminated. There is always a minimal residual risk, even with the highest quality standards.
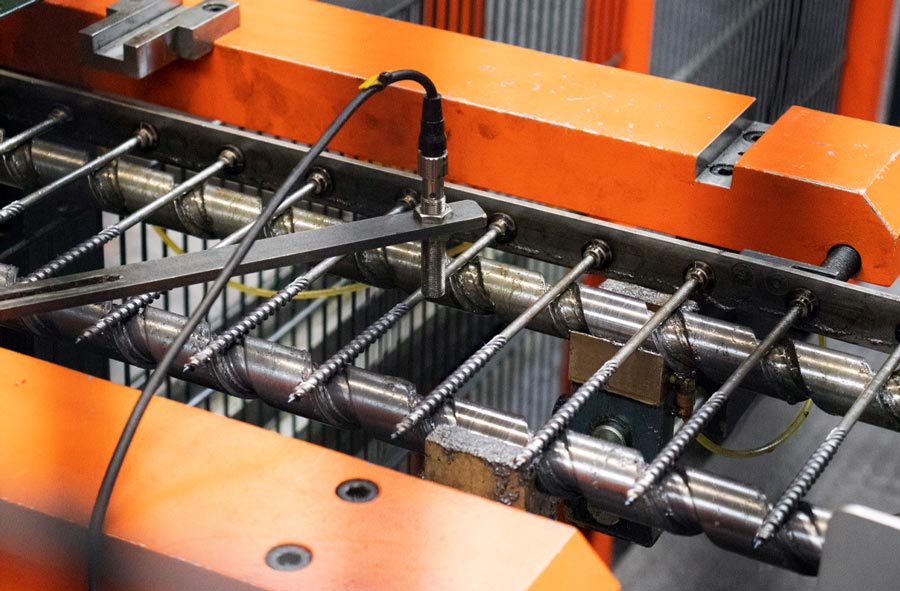
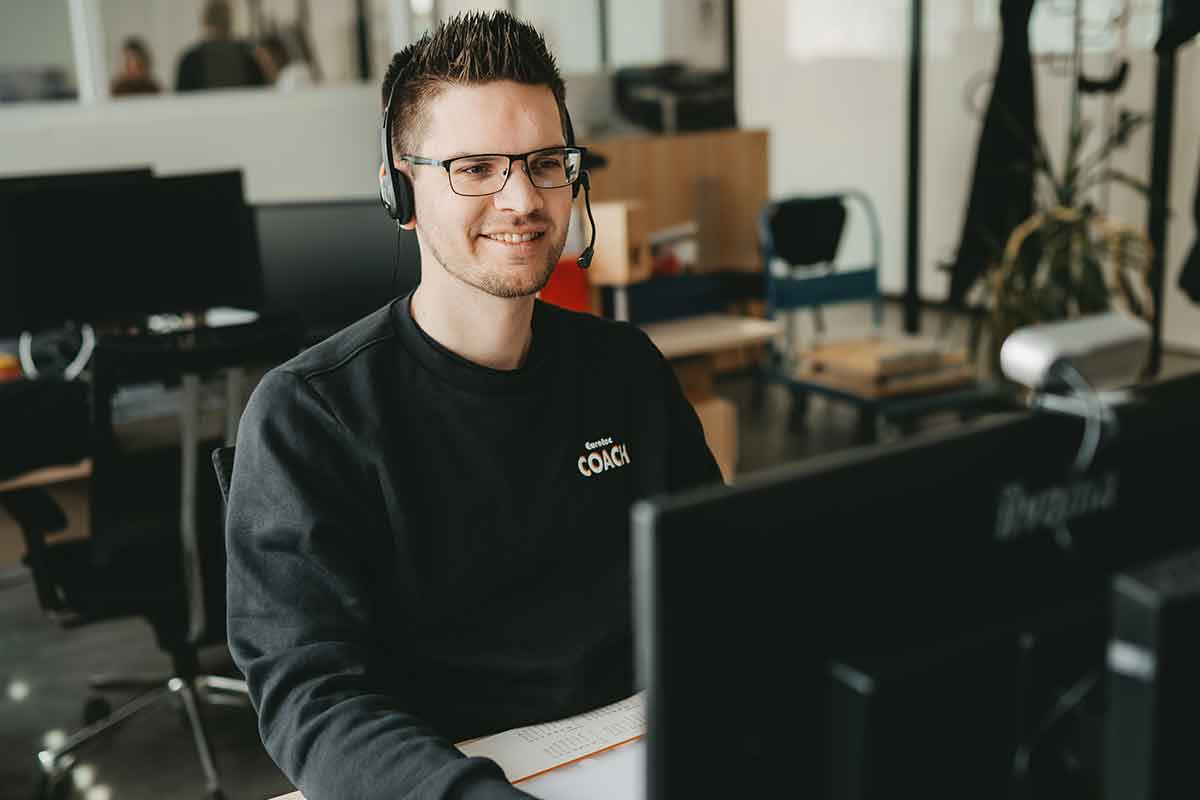
Would you like to find out more information on this topic?
Contact our technical department by email at technik@eurotec.team or by phone on +49 2331 6245-444 and let us advise you.
Other technical articles
Here you will find further specialist articles with comprehensive content that you need to know on the construction site or for individual projects - regardless of whether you are just starting out or already have many years of experience.