Production
Our production is versatile - see for yourself!
From incoming goods to quality control - at Eurotec we rely on innovative production using the latest technologies to meet our customers’ highest demands. Our company is made up of around 4,000 m² of production area, including outdoor storage space.
For the production of fully threaded screws, we benefit above all from our all-in-one machine, which covers the processes from cutting to depositing the finished screws.
Welcome to Eurotec – your partner for innovative fastening solutions!
For over 25 years, we have stood for quality and innovation in the construction sector. Whether it's timber construction, decking, or concrete fastening – our products provide the foundation for your best projects.
As a medium-sized company, we focus on proximity, quality, and the best solutions for you. Through our trading partners, our products reach exactly where you need them – quickly, reliably, and always ready to help you achieve great things.
Eurotec – fastening technology that connects.
Stamping and stampingbending technology
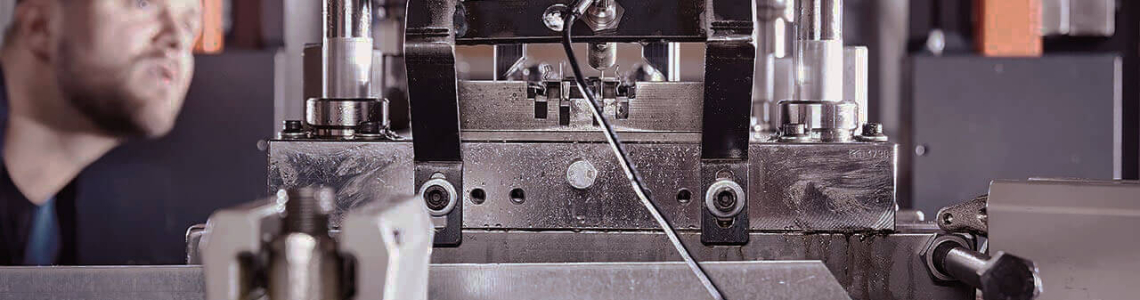
Punching and punch-bending technology is one of our main areas of expertise. With the help of this technology, we manufacture holistic solutions for our customers’ most diverse applications worldwide.
Eccentric presses are available from 40 to 400 tonnes pressing force and a maximum of 400 strokes per minute. With these high-performance machines, tape widths of up to 500 mm and tape thicknesses of 0.15 - 8 mm are possible. Production is primarily from coil with specially designed follow-on cutting or follow-on composite tools. With the help of the punching and punch-bending technique, rhombus clips, cladding clips or shear angles are produced, among other things.
Do you have any further questions? Our experts will be happy to advise you comprehensively on your choice of material and surface. A wide range of options and designs are possible here in order to find the perfect solution for every area of application. The focus is always on close cooperation with our customers in order to fulfil their wishes and requirements in the best possible way.
Whatever your requirements, with us you get everything from a single source.
Cold forming
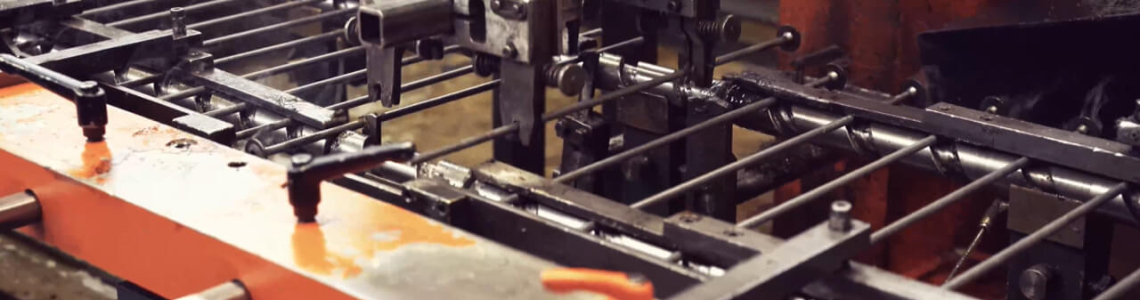
At Eurotec we bring your components into shape!
Since the start of production in 2013, production has been steadily expanded in order to manufacture an ever-increasing proportion of long-cycle cold-formed parts at our Hagen site. These include a number of special construction screws, for example, including the KonstruX fully threaded screws or Topduo roofing screws. Our modern machinery enables us to produce screws economically in one pass. This makes it possible for machines to automate up to eight machining steps.
The wire supplied to the coils is first straightened and then cut to length. We make cold formed parts with a diameter of up to 16 mm and a length of up to 3,000 mm in our production facility. The screw head is pressed in two stages, pre-heading and finishing. The thread is then rolled on. Milling of the type 17 scraping groove takes place directly during the process. At the end, the manufactured screws are placed in transport containers in an orderly manner by a robot.
10 steps to the perfect screw
In this video, we take you through the production and processing of our screws in 10 steps: from wire drawing and preparation, length division, head forming, and thread rolling, to hardening, galvanization, quality control, and finally packaging and assembly. This detailed walkthrough gives you valuable insights into Eurotec's manufacturing process.
Injection moulding
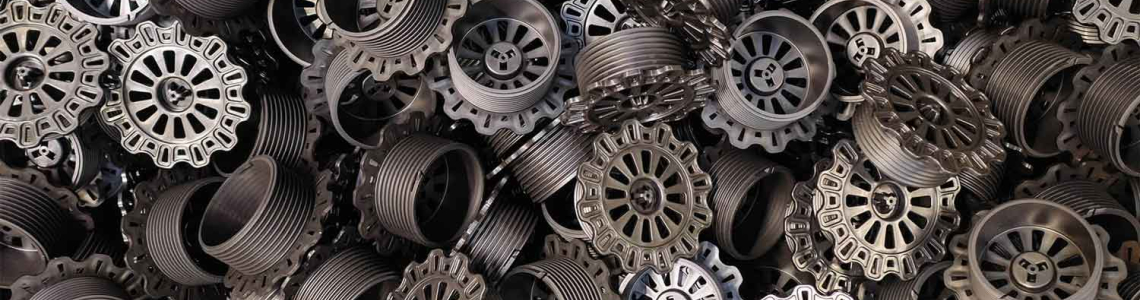
We can also make use of our many years of experience in the field of plastic injection moulded parts at our location in Hagen. We are ISO 9001 quality management certified. In order to increase the satisfaction of our customers, quality inspections and monitoring are carried out at regular intervals. Our production range includes multi-dimensional plastic injection moulded parts, such as the Profi-Line adjustable pedestals and various adapters. These are particularly beneficial due to their weather resistance and durability. In 2019, we produced approximately 900,000 adjustable feet and 1 million decking clips.
Thanks to the modern machinery with a total of eight injection moulding machines for production, it is possible to process a wide range of thermoplastics depending on requirement and application.
We are able to produce any kind of plastic parts - not only industry-related products. Our machines work with holding forces from 30 to 220 tonnes.
All of the machinery was moved to a new production hall in early 2018 due to continuous expansion.
Extrusion technology
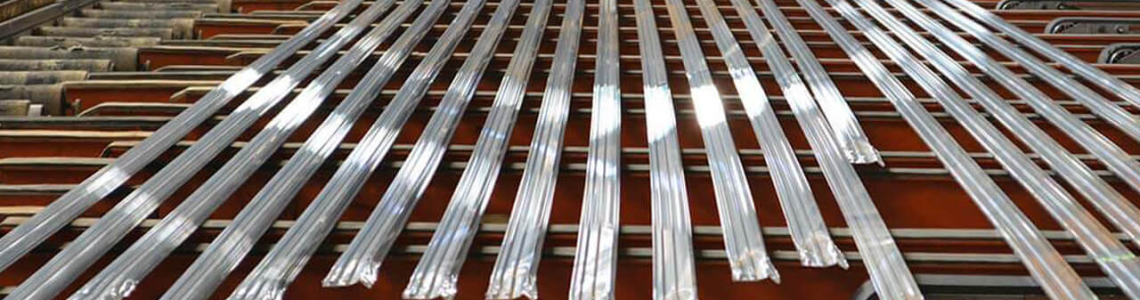
In the extrusion process, raw materials are heated and pressed under pressure using a shaping tool. The typical extrusion alloy is EN AW 6063. The result is a straight strand that can be cut to length as desired. All aluminium system profiles in our product range, such as the EVO or Eveco aluminium system profile, are manufactured using extrusion technology. This process is also used for WPC decking boards.
The main advantages are that very complex shapes can be produced in long lengths and extremely precisely. Dimensions range from one to six metres.