Wood construction screw manufacture
Wood construction screw manufacture
For more than 20 years now, Eurotec GmbH has been a renowned specialist in fastening technology, offering its customers a multifaceted product range. This includes fastening systems for wood, façade and concrete construction and terrace substructures, tools for manual workers and in-house screw production.
In-house production at our Hagen site
Eurotec uses innovative production methods with cutting-edge technology. With its internal screw production in the areas of punching and punch & bend technology, cold forming, plastic injection moulding and extrusion technology, the company is highly diversified and can therefore ensure quality control and optimal implementation of its customers’ stringent quality standards.
Creating the perfect wood construction screw, step by step
How are wooden construction screws manufactured at Eurotec?
To manufacture screws, the companies has its own cutting-edge machinery to enable all individual customer requirements to be met. The manufacturing of a screw always begins with selecting a suitable raw material. Cold heading wires with high carbon content are widely used, which can be hardened at a later stage. The cold heading wire is pre-drawn in a wire drawing shop and then fully drawn to the nominal size.
This is followed by the screw manufacture itself. The wound wire coils are fed into the machine with a decoiler. The wire is flattened by straightening units and cut to the appropriate lengths.
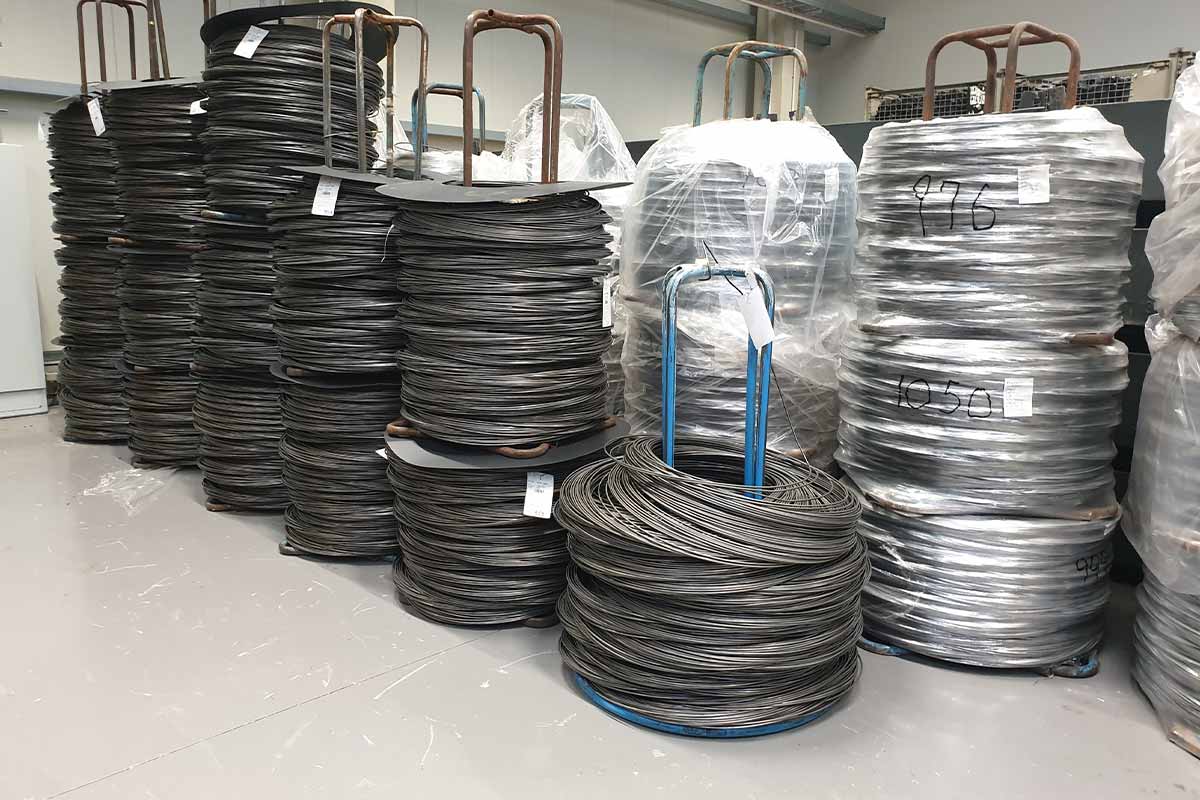
In the next step, the screw head and drive shapes are formed by double-blow presses. This involves pre-compression to create the volume, followed by final compression to form the geometry.
After this, a thread is rolled onto the surface by flat die rollers. For this procedure, a screw blank is pushed into a stationary thread rolling die and drawn by a moving thread rolling die. The thread reflects the negative impression of the rolling dies. Various types of thread can be produced using flat rollers or plain rollers. Plain rollers are used to manufacture fully threaded screws.
We have made it our mission to continuously optimise our tools in order to achieve the best possible results when our diverse screws are used, ensuring, for example, that screws can be driven in quickly and with reduced force, so that cordless screwdrivers need recharging less often and there is less cracking in the wooden construction material.
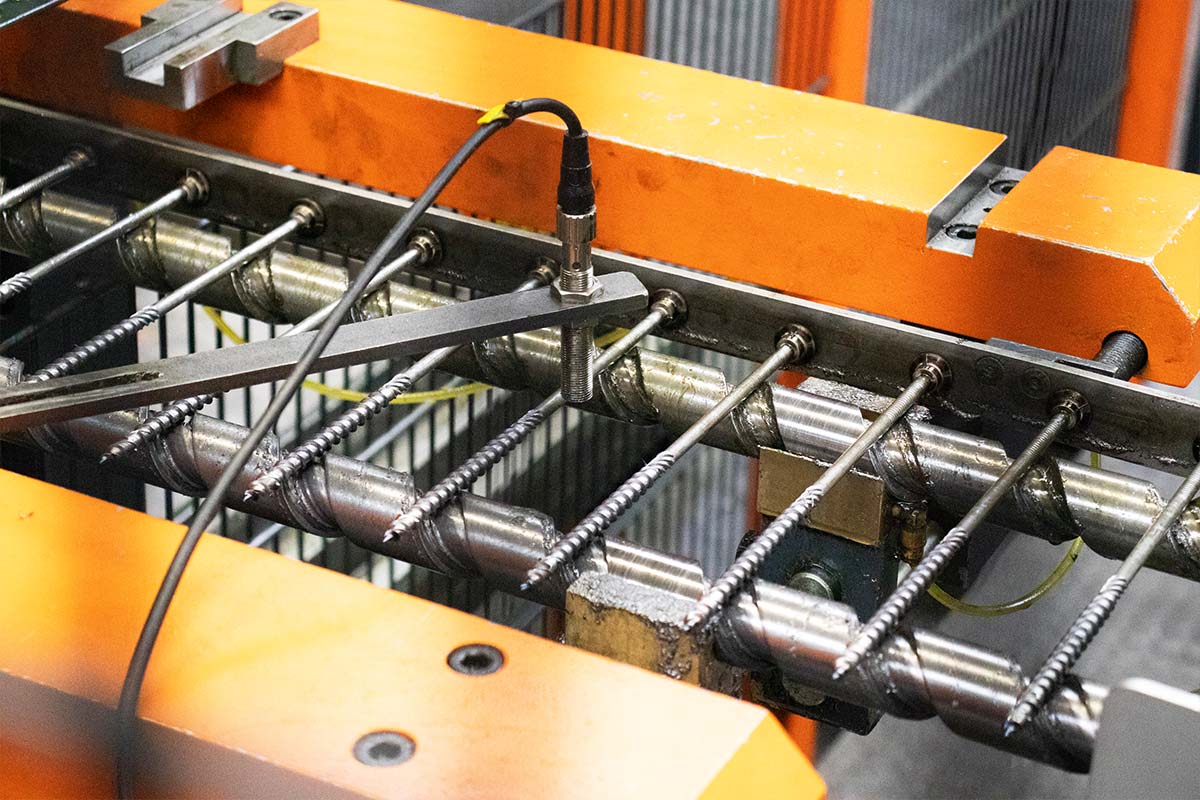
The final manufacturing steps
In the final stage, the manufactured screws are case-hardened to achieve both high surface hardness and a high breaking torque. The screws are then annealed. This procedure is necessary to homogenise the metal’s microstructure. This enables the screw to bend to a certain angle without breaking.
To protect the screws from corrosion, they are electrogalvanised. They are also given an anti-friction coating that is intended to further increase the corrosion protection and to make the screw easier to screw in.
Lastly, the wood construction screws are packaged appropriately and prepared for dispatch. They are now ready to be used for all kinds of wood construction projects.
You will find more information about our wood construction screws on our website.
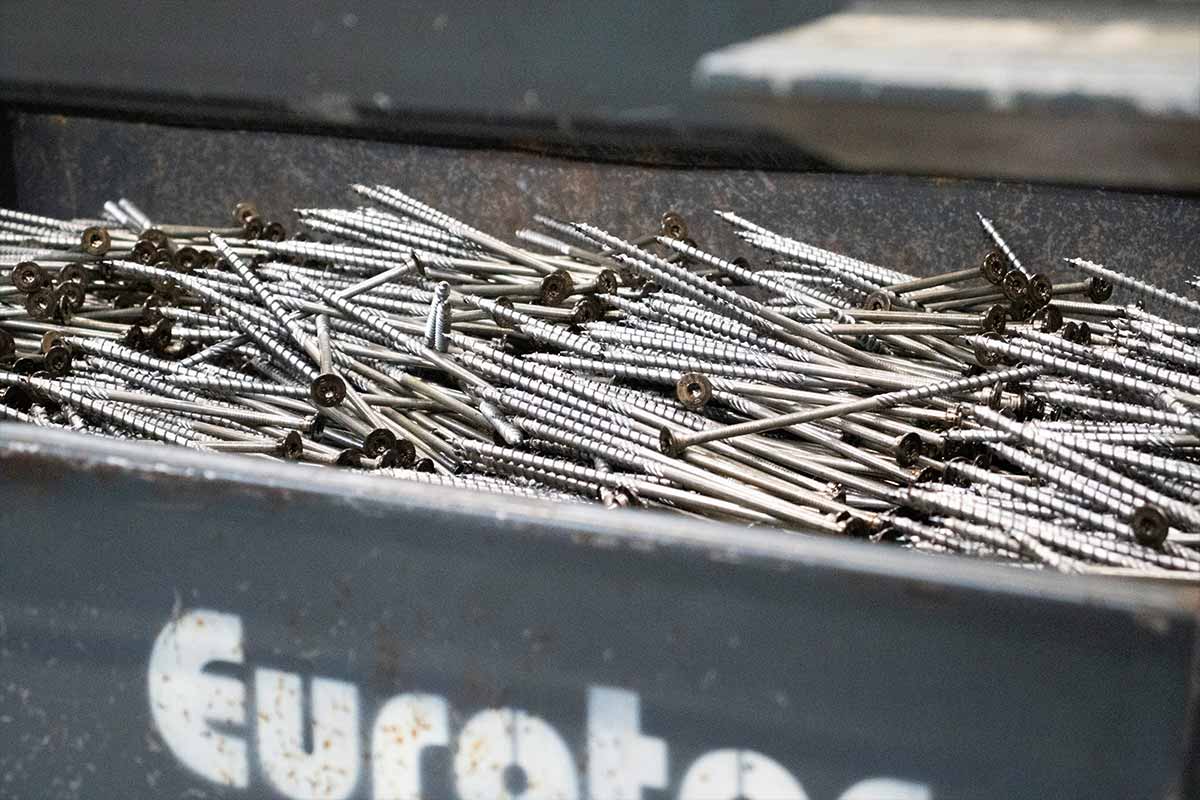
Media library
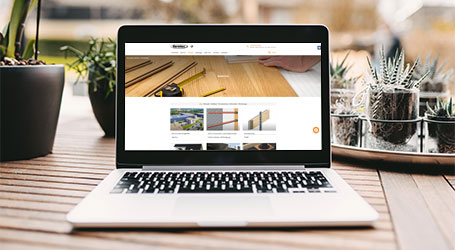
Media library
You will find all product presentations and application videos in our media library. How do I build a substructure? Is it possible to fix terrace decking in a non-visible way? And if so, how? Answers to these questions and much more can be found in our informative videos.
Other news
Here you will find information and news about Eurotec.
Discover new catalogues, products or other topics.
-
News
Do you always want to be up to date? In our news section you will get an exclusive insight into our company. Read it now!
более -
About us
Get to know us! At Eurotec, we offer our customers a broad product portfolio and many years of experience.
более -
Contact
If you require further details, please call us on +49 2331 6245-0 or send us an email. We are happy to help!
более
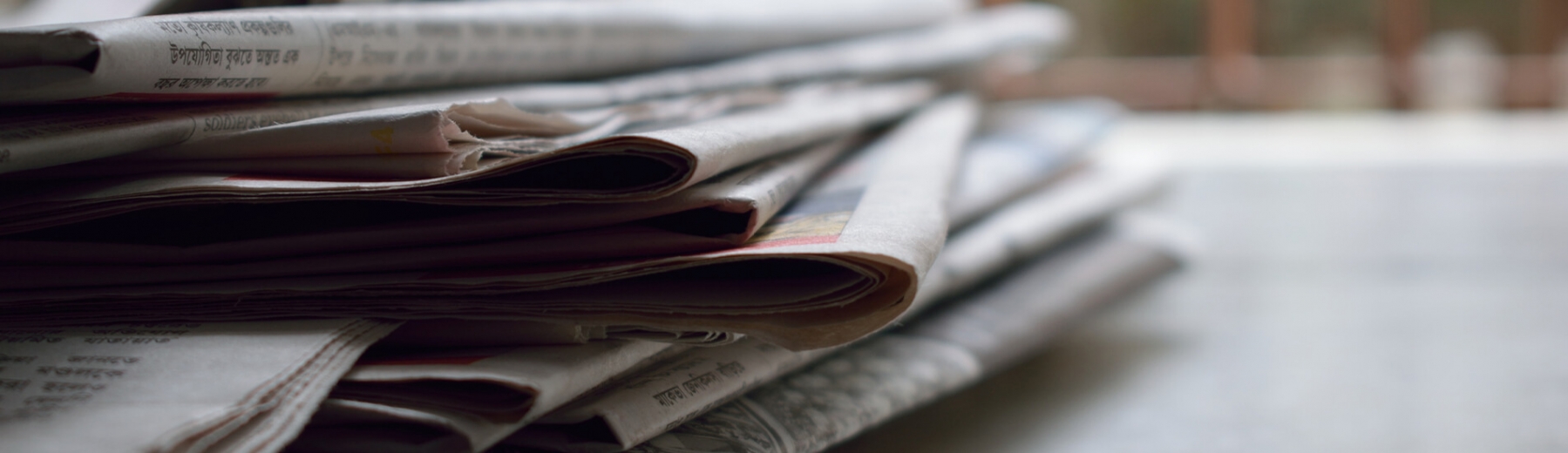