Sistema de Revestimientos para Tornillos de Construcción con Madera
Sistema de Revestimientos para Tornillos de Construcción con Madera
¿Cuál es el límite de uso de los tornillos de acero al carbono en la clase de servicio 3 de la construcción con madera? Nosotros, de Eurotec, como especialistas en tecnología de la fijación, hemos tratado este tema y hecho un extenso trabajo de investigación para poder brindar conclusiones fehacientes y recomendaciones prácticas de manera idónea.
El objetivo de este estudio práctico fue analizar los requisitos de norma, para luego identificar los sistemas de revestimiento adecuados y llevar a cabo pruebas de corrosión en muestras de varios tipos de tornillos revestidos.
Base teórica:
Clases de servicio en la construcción con madera:
La norma EN 1995-1-1 define tres clases de servicio para la construcción con madera.
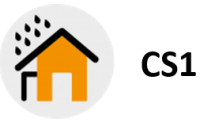
Clase de servicio 1: interior, no expuesto a la intemperie. Seco
Esta clase de servicio se caracteriza por un contenido de humedad de los materiales de construcción correspondiente a una temperatura de 20 °C y una humedad relativa del aire circundante que excede el valor de 65% solamente por algunas semanas al año. En la CS1, el contenido de humedad promedio de la mayoría de las maderas de coníferas no excede el 12%, como p. ej. en ambientes cerrados y calefaccionados en todos sus lados.
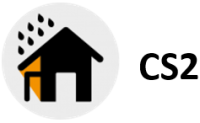
Clase de servicio 2 (CS2): interior, ambiente húmedo, y exterior, bajo cubierta. Ocasionalmente húmedo
Esta clase de servicio se caracteriza por un contenido de humedad de los materiales de construcción correspondiente a una temperatura de 20 °C y una humedad relativa del aire circundante que excede el valor de 85% solamente por algunas semanas al año. En la CS2, el contenido de humedad promedio de la mayoría de las maderas de coníferas no excede el 20%, como p. ej. en ambientes semicubiertos.
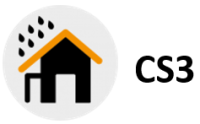
Clase de servicio 3 (CS3): exterior, expuesto a la intemperie. Predominante o permanentemente húmedo
Esta clase de servicio presenta condiciones ambientales que llevan a contenidos de humedad superiores a los de la CS2, como p. ej. en conexiones con exposición directa a la intemperie.
Requisitos de los sistemas de revestimiento según EN 1995-1-1
Los tornillos metálicos y demás conectores estructurales de dicho material deberán ser, si se lo requiere, inherentemente resistentes a la corrosión o estar protegidos contra la corrosión.
En el caso del galvanizado en caliente, las aleaciones de Fe/Zn 12c y de Fe/Zn 25c deberán ser reemplazadas por Z275 y Z350, respectivamente. Para condiciones de corrosión particularmente agresivas, se deberá considerar un mayor grosor de galvanización o el uso de acero inoxidable.
Otros requisitos para los sistemas de revestimiento se definen en la norma EAD 130118-01-0603 "Tornillos y barras roscadas para uso en la construcción con madera". En el sub ítem 2.2.12.3 "Protección alternativa contra la corrosión" se indican posibles desviaciones respecto a la protección contra la corrosión indicada en los ejemplos de la EN 1995-1-1. Es necesario evaluar la equivalencia de protección necesaria, considerando la categoría de corrosividad permitida de acuerdo con la norma DIN EN ISO 12944-2. Las condiciones ambientales atmosféricas se dividen en seis categorías de corrosividad: C1 a C4, y luego C5-I y C5-M.
Además de ello, deben llevarse a cabo testeos al aire libre durante un período de al menos cinco años. De esta manera, resulta teóricamente posible emplear tornillos para construcción en madera hechos de acero al carbono en la CS3 contando con el sistema de recubrimiento correspondiente, pero aquí también deben tenerse en cuenta las condiciones ambientales de servicio.
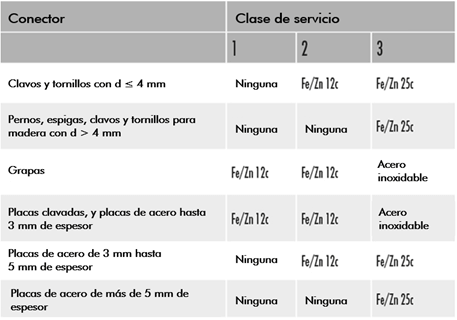
Procedimiento de ensayo:
Para testear los materiales con sus recubrimientos protectores, se realizan pruebas de corrosión cíclicas. Mediante procedimientos y equipos estandarizados, es posible lograr resultados fehacientes y de uso práctico en tiempo relativamente cortos.
El ensayo de aclimatación constante, según DIN EN ISO 9227 NSS, es un método de prueba simplificado. Las probetas son rociadas con una solución salina al 5% NaCl en condiciones ambientales de 35 °C y 100% de humedad relativa. La duración del ensayo puede ser de 6 horas hasta 1000 horas o más, dependiendo del requisito de resistencia a la corrosión. El ensayo de niebla salina es un método de prueba comúnmente aceptado para el control de calidad de recubrimientos en la industria.
El ensayo de Kesterich, según DIN 50018, pertenece al grupo de pruebas de aclimatación variable. Las probetas se exponen a una mezcla de aire caliente y húmedo con óxido de azufre. La prueba se divide en ciclos de 24 horas cada uno. Las probetas se consideran aprobadas si logran alcanzar un determinado número de ciclos sin presentar un tipo de oxidación específico.
En el ensayo de condición higrotérmica variable PV1209, las probetas son rociadas con una solución salina al 4% NaCl y 1% CaCl2. La temperatura ambiente varía en el rango de -40 °C a +80 °C, con una humedad relativa variable entre 30% y 95%. Un ciclo de testeo de este ensayo dura una semana.
Las pruebas de corrosión cíclicas brindan información sobre la evaluación y optimización de la resistencia a la corrosión. La degradación diaria real es simulada de forma simplificada en estos ensayos, y, por lo tanto, no representa la degradación y agresividad de aquella en toda su complejidad. Un testeo de niebla salina representa solamente una de las tantas condiciones extremas a las que se encontrarán sujetos los elementos en servicio. Tampoco existe una correlación entre los diferentes métodos de ensayo. Por eso, las pruebas reales al exterior también son importantes. Sin embargo, estas requieren gran cantidad de tiempo de exposición a la intemperie para lograr obtener resultados confiables.
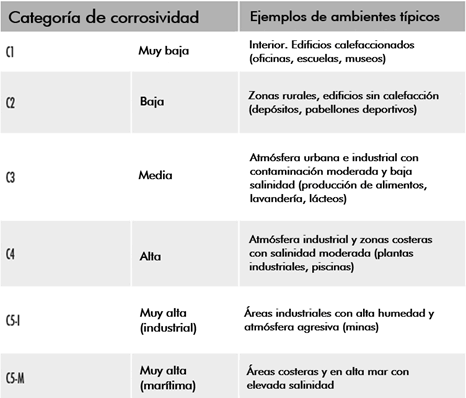
Conceptos básicos de los sistemas de revestimiento:
Los recubrimientos superficiales en tornillos y conectores son la protección primaria contra la corrosión. El Zinc el usualmente usado para este fin. Como la corrosión es un proceso químico y el zinc es menos noble que el hierro, se lo utiliza como un ánodo de sacrificio, protegiendo al hierro antes de que este se corroa por completo. Luego, sellados y capas adicionales pueden conformar protecciones adicionales.
En el proceso de recubrimiento galvánico, los cationes metálicos se depositan catódicamente sobre los componentes en electrolitos acuosos bajo el flujo de corriente. Esto se realiza en tambor o en bastidores especiales. Los recubrimientos metálicos pueden ser de zinc, níquel o acero. También se utilizan recubrimientos con aleaciones de zinc-níquel o zinc-hierro, por ejemplo.
El recubrimiento de escamas de zinc es un recubrimiento no electrolítico hecho de sistemas de pintura a base de solventes. Aquí se utilizan procesos de inmersión o pulverización, “pintando” los componentes. Los elementos metálicos que se aplican son zinc o aluminio, y las laminillas de metal se encuentran en un sistema aglutinante. Los disolventes se evaporan durante el proceso de cocción y el aglutinante se entrecruza. Los sistemas de escamas de zinc se conocen en el mercado con varios nombres sinónimos, tales como "Geomet", "Dacromet", "Delta" o "Ruspert". La variación del grosor de deposición del recubrimiento es elevada, lo que significa que lograr una capa homogénea es casi imposible con estos sistemas de escamas de zinc.
Una comparación directa de los dos sistemas de recubrimiento muestra que la dureza aumenta desde la lámina, a través del recubrimiento de zinc, hasta el recubrimiento de zinc-níquel. Un recubrimiento de zinc-níquel promete una resistencia a la corrosión muy elevada. Por otro lado, el riesgo de fragilización por hidrógeno es alto en los recubrimientos galvánicos. Cuanto mayor es el espesor de la capa, mayor es el riesgo de fragilización por hidrógeno. Los recubrimientos laminares no son muy resistentes a la abrasión y son susceptibles a daños mecánicos. El proceso de transporte y embalaje conduce al deterioro del recubrimiento. Por ello, los resultados de las pruebas solo pueden realizarse en muestras directamente después de la producción, y entonces, los resultados no resultan representativos.
En el galvanizado por inmersión en caliente, los componentes se sumergen en zinc fundido a una temperatura entre 455 °C y 480 °C (galvanización a temperatura normal), o entre 530 °C and 560 °C (galvanización a altas temperaturas). La gran ventaja es el alto grado de penetración del recubrimiento en el material base. El grosor medio de la capa de zinc se encuentra entre 50 µm y 150 µm. El galvanizado en caliente brinda una protección económica contra la corrosión por décadas, sin necesidad de manutención. Sin embargo, este método no es apto para usarse en tornillos para madera de acero endurecido.
Durante el proceso de ennegrecimiento, los componentes se sumergen en una solución salina alcalina caliente, creando una película de óxido negra muy homogénea. La capa azulada es una capa de conversión del óxido negro. Los conectores de óxido negro tienen un bajo nivel de protección contra la corrosión.
Durante el fosfatado, los componentes se sumergen en una solución de fosfato. Aquí, los tipos de recubrimiento pueden ser fosfatos de hierro, manganeso, zinc, y zinc/calcio. Los tornillos fosfatados tienen propiedades de fricción mejoradas. Su apariencia varía de gris claro a negro.
El acero inoxidable es usualmente utilizado en ambientes expuestos a la intemperie. Existen distintos tipos de acero inoxidable. Las categorías más comunes son el C1, A2 y el A4. El acero inoxidable C1 posee propiedades mecánicas similares al del acero al carbono y, adicionalmente, posee buena resistencia contra la corrosión. El acero inoxidable A2 posee una mejor resistencia a la corrosión que el anterior, y una resistencia razonable a los ácidos. Finalmente, el acero inoxidable A4 posee una resistencia a la corrosión y a los ácidos excepcional, superior a los anteriores.
Por lo tanto, el acero inoxidable es el material ideal para el servicio al exterior, pero es significativamente más costoso, y goza de propiedades mecánicas peores que el acero al carbono. En ese sentido, se encuentran disponibles en el mercado varias soluciones de recubrimiento para elementos de acero al carbono comprobadas para uso en CS3.
Testeo de los sistemas de revestimiento
Para probar diferentes sistemas de recubrimiento ofrecidos en el mercado, organizamos muestras aleatorias. Se testearon cuatro tipos distintos de recubrimiento que aseguran ser aptos para su uso en CS3. Cada uno de ellos se anuncia de diferente manera en el mercado. La investigación incluyó la realización de micro cortes transversales en las muestras para evaluar la estructura de la capa protectora. Además, también se compró la resistencia a la corrosión con ensayos de niebla salina. Este estudio práctico considera los efectos posproducción de transporte y embalaje de los tornillos.
La Muestra 1, con recubrimiento galvanizado electrolítico (probablemente de zinc-níquel), se anuncia como apta para categoría de corrosividad C4H/C5M y promete una resistencia a la corrosión de 2000 horas en el ensayo de niebla salina. Lo que se destacó visualmente fue la homogeneidad del recubrimiento. La aparición de óxido rojo comenzó luego de 1224 horas de iniciado el ensayo.
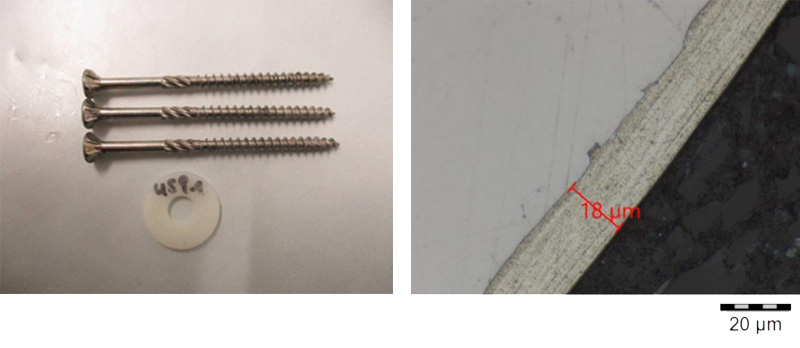
La Muestra 2, con revestimiento de escamas de zinc, se anuncia como apta para la categoría de corrosividad C4 y promete una resistencia a la corrosión de 1000 horas en el ensayo de niebla salina. A pesar de que el grosor de la capa protectora se mostró uniforme, la formación de óxido rojo ya se hizo visible a partir de las 672 horas de ensayo.
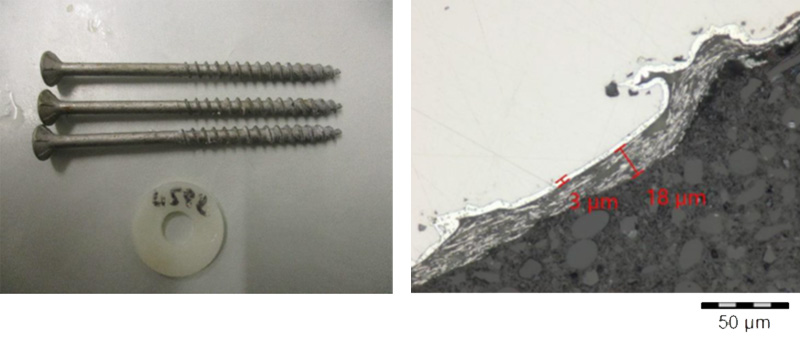
La Muestra 3, con revestimiento de escamas de zinc, se anuncia como apta para la categoría de corrosividad C4 y promete una resistencia a la corrosión de 1500 horas en el ensayo de niebla salina. Se comprobó una distribución pobre de la capa protectora, y la aparición de óxido rojo ocurrió tan sólo 24 horas de empezado el ensayo.

La Muestra 4, con revestimiento de escamas de zinc, promete una resistencia a la corrosión de 1000 horas en el ensayo de niebla salina. También se observó una capa protectora muy dispareja, y el óxido rojo se hizo aparente luego de 384 horas de ensayo.
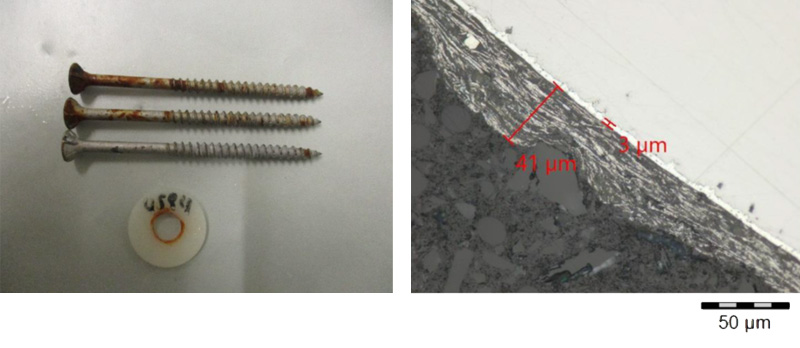
Finalmente, estos experimentos confirmaron la dificultad de obtener una protección homogénea con sistemas de recubrimiento con escamas o laminillas de zinc. Este método de protección ciertamente logra con cumplir los requisitos de resistencia bajo condiciones de laboratorio inmediatamente después de su producción, soportando gran cantidad de horas en las pruebas de niebla salina. No obstante, en la realidad, luego de los procesos de transporte y embalaje, estos valores no se alcanzan ni siquiera de manera aproximada. El recubrimiento que tuvo mejor desempeño en estos experimentos fue el de la Muestra 1, de galvanización electrolítica.
Entonces, uno de los factores de riesgo para el recubrimiento de un tornillo es el daño producido durante el transporte y embalaje, siendo su cabeza el punto más débil. Los sistemas de escamas de zinc son particularmente susceptibles a estos daños, ya que las pequeñas virutas afectan la capa protectora. Las condiciones ambientales son otro factor de riesgo parar los recubrimientos. Por ello, el uso de acero inoxidable o de acero galvanizado en caliente es esencial en áreas costeras. Incluso la propia madera puede resultar ser un factor de degradación para los metales. Los diferentes componentes y extractivos que se encuentran en el interior de la madera pueden influenciar el desempeño de los recubrimientos.
Con el conocimiento obtenido de los experimentos anteriores, se desarrollaron cinco sistemas de recubrimiento diferentes para nuestros tornillos y luego se realizó un muestreo de estos. Luego, las muestras se sometieron al ensayo de corrosión variable PV1209, teniendo como objetivo/requisito que las mismas resistan por lo menos cuatro ciclos. La siguiente tabla presenta una descripción general:
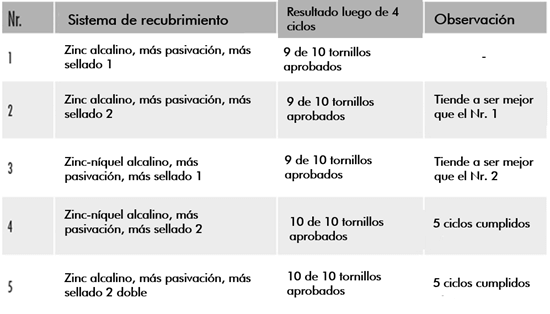
Luego de revisar y comprar los resultados, el sistema de recubrimiento No. 5 es el que demostró mejor desempeño y, por ende, el recomendado. Esto también se hace evidente al comparar visualmente las muestras luego del ensayo.
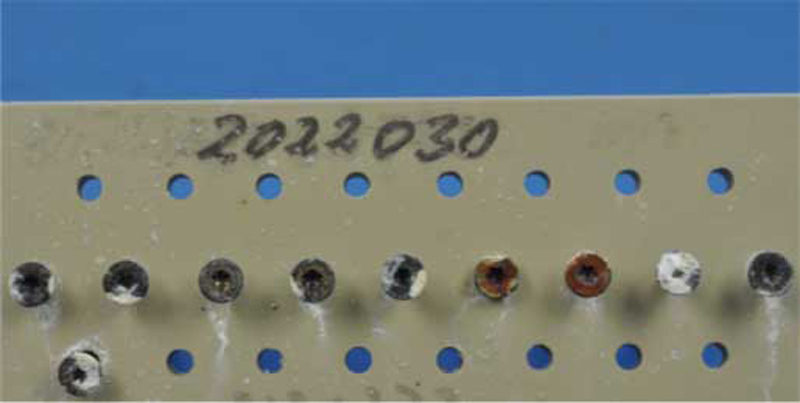
Muestra No. 2: zinc alcalino, más pasivación, más sellado 2
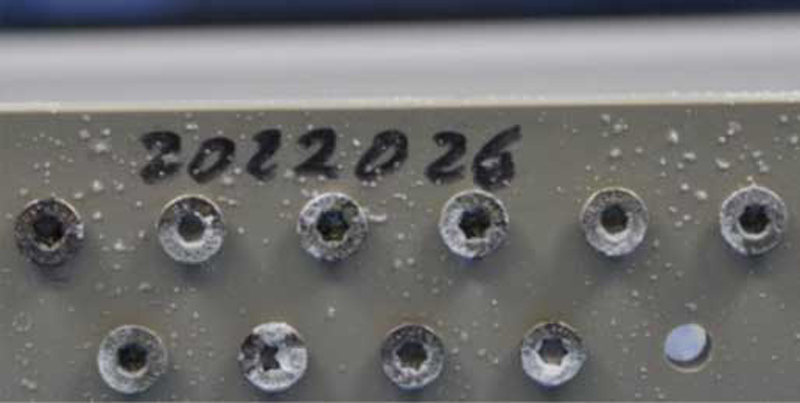
Muestra No. 5: zink alcalino, más pasivación, más sellado 2 doble
Comportamiento de las muestras en el ensayo a largo plazo
De modo a poner a prueba nuestros tornillos de la forma más práctica posible, también realizamos una prueba de muy larga duración. Para ello, en febrero de 2011, atornillamos varias muestras de ellos en madera de Garapa y los dejamos completamente expuestos a la intemperie.
Se realizó un análisis preliminar pasados solamente dos años, donde se comprobó que los tornillos de acero inoxidable A2, A4 y C1 seguían viéndose impecables. Tampoco se observaron anormalidades en el tornillo con recubrimiento especial PT 1000. Sólo los tornillos galvanizados amarillos presentaron un inicio de formación de óxido rojo en sus cabezas.
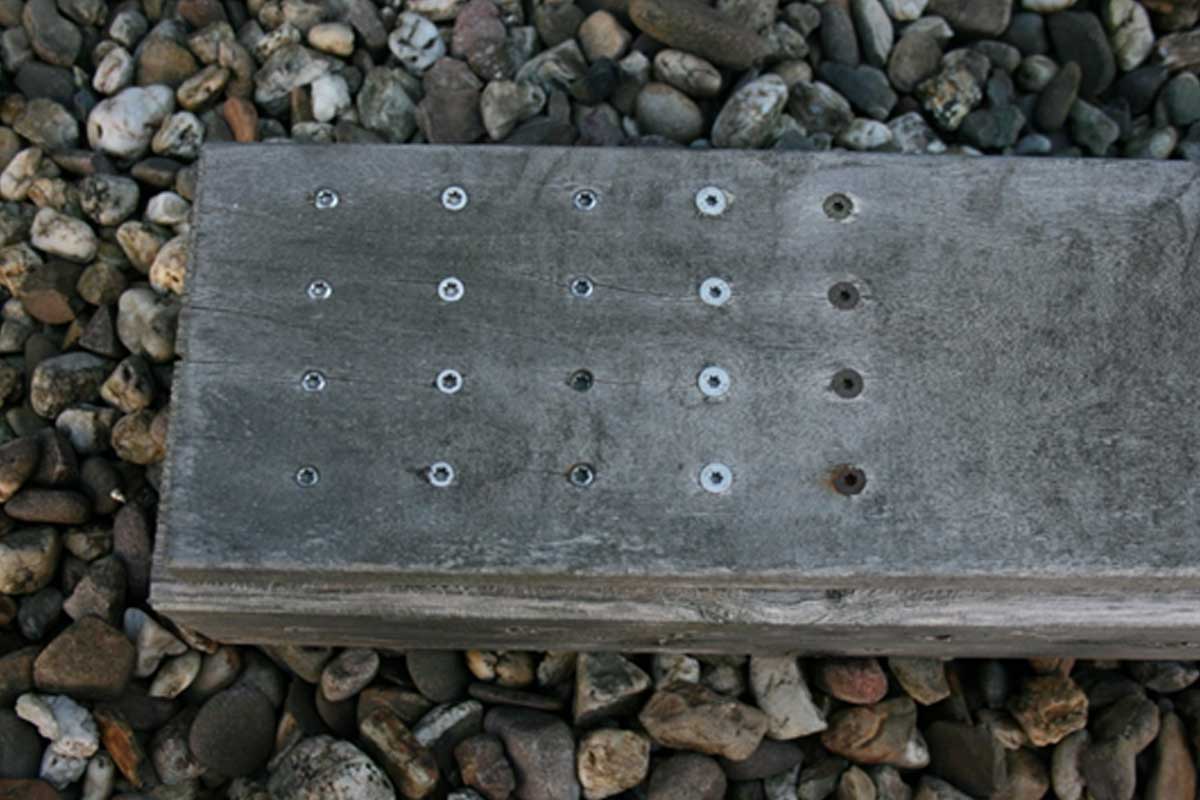
Foto tomada en 19.07.2013 (de izquierda a derecha: A4 – A2 – C1 – PT 1000 – Galvanizado amarillo)
Estas fotografías se tomaron casi once años luego de la prueba al exterior
Luego de 11 años, es posible obtener resultados significativos. Los tornillos de acero inoxidable A2 y A4 aún se encontraban muy bien, y los tornillos de acero inoxidable endurecido C1 presentaban un manchado parcial en sus cabezas, probablemente debido a los extractivos de la madera de Garapa.
Las cabezas de los tornillos con recubrimiento especial PT 1000 aún no presentaban óxido. Por otro lado, su parte roscada se vio parcialmente afectada por óxido rojo. Hay que mencionar que la madera utilizada en el experimento se encontraba severamente degradada y resquebrajada por el largo paso del tiempo expuesta a la intemperie, dejando a los tornillos atornillados aún más vulnerables. Por sorpresa, inclusive los tornillos galvanizados amarillo, los cuales solo están aprobados para usarse en CS1 y CS2, no se vieron severamente afectados por óxido rojo en su parte roscada y fuste. De manera general, en la práctica, los tornillos se ven protegidos en todo su largo por la madera que los rodea, y por eso evaden en gran medida los procesos de corrosión.
La madera, la cual no estuvo protegida de ninguna madera durante este experimento a largo plazo, se vio mucho más desgastada que los tornillos. Esto coincide con lo especificado en el Eurocódigo 5 (EN 1995-1-1). De acuerdo con el mismo, los tornillos con diámetro mayor que 4 mm no necesitan protección adicional cuando empleados en CS1 y CS2. Aquí, la madera protegió a los tornillos de tal manera que los mismos sufrieron ninguna o muy poca corrosión. Aun así, con frecuencia, pero casi siempre, los tornillos se protegen contra la corrosión, sin importar el tamaño de su diámetro o clase de servicio, mayoritariamente por motivos estéticos.
Como un próximo paso, podría haberse mejorado el desempeño de los tornillos aún más de estar protegida la pieza de madera atornillada, estando cubierta o tratada con preservantes apropiados. De esta madera, se evita o mitiga la posibilidad de que la madera se pudra, e por consecuencia, que la humedad llegue a los tornillos y provoque con el tiempo la aparición de óxido rojo. Por consiguiente, la protección de la madera es también un requisito de suma importancia, y debe realizarse con el cuidado debido y paulatino, tanto como su condición de servicio lo requiera.
Pérdida/desgaste del material como resultado de la corrosión en aceros sin alear
Asumiendo condiciones ambientales urbanas o industriales, (clase de corrosividad C3, según EN ISO 12944-2) con contaminación moderada, un tornillo de acero sin alear (ignorando el recubrimiento) verá una reducción de su grosor de 25 a 50 µm/año en el primer año de exposición.
El siguiente ejemplo puede usarse para indicar la pérdida de masa/grosor de material relativa luego del primer año de exposición:
Mín. pérdida de material por año: 25 (µm)/año = 0,025 mm/año
Máx. pérdida de material por año: 50 (µm)/año = 0,05 mm/año
Si se asume que la mayor pérdida de material ocurre durante el primer año de exposición y con una progresión lineal, puede realizarse el siguiente cálculo:
Diámetro del fuste de tornillo Ød0= 4,4 mm
Diámetro mínimo funcional de fuste del tornillo ØdE= 4 mm
Máxima pérdida de material:
(Ø4,4mm - Ø4mm)/2 = 0,2 mm
Durabilidad teórica máx. = 0,2mm/(0,025mm/año) = 8 años (*)
Durabilidad teórica mín. = 0,2mm/(0,05mm/año) = 4 años (*)
Independientemente de la resistencia a la corrosión del revestimiento, la vida útil teórica del tornillo (ignorando el recubrimiento) puede asumirse entre 4 y 8 años (*).
(*) No obstante, este valor es influenciado por la tensión mecánica a la que esté sujeto el tornillo y la variación de las condiciones ambientales de servicio, por lo tanto, el mismo no puede garantizarse.
Finalmente, este estudio permite registrar observaciones importantes. Con el recubrimiento apropiado, es posible emplear tornillos de acero carbono en CS3. Sin embargo, esto no debe tomarse como una recomendación general. En condiciones de servicio menos agresivas, y utilizando madera de una especie con menor cantidad de extractivos corrosivos, es razonable utilizar este tipo de tornillos. En cambio, en un ambiente altamente corrosivo, p. ej. cerca de la costa del mar o al utilizar madera con gran cantidad de taninos (como el roble), es esencial emplear acero inoxidable. Algunas especies de madera dura (latifoliadas) contienen substancias que, bajo ciertas condiciones, pueden corroer fuertemente los tornillos y barras roscadas de conexiones. Bajo estas circunstancias, debe emplearse sin dudas por lo menos un acero inoxidable A2 o A4.
Visite nuestro sitio web para obtener más información útil y datos técnicos sobre los tornillos para madera Eurotec.
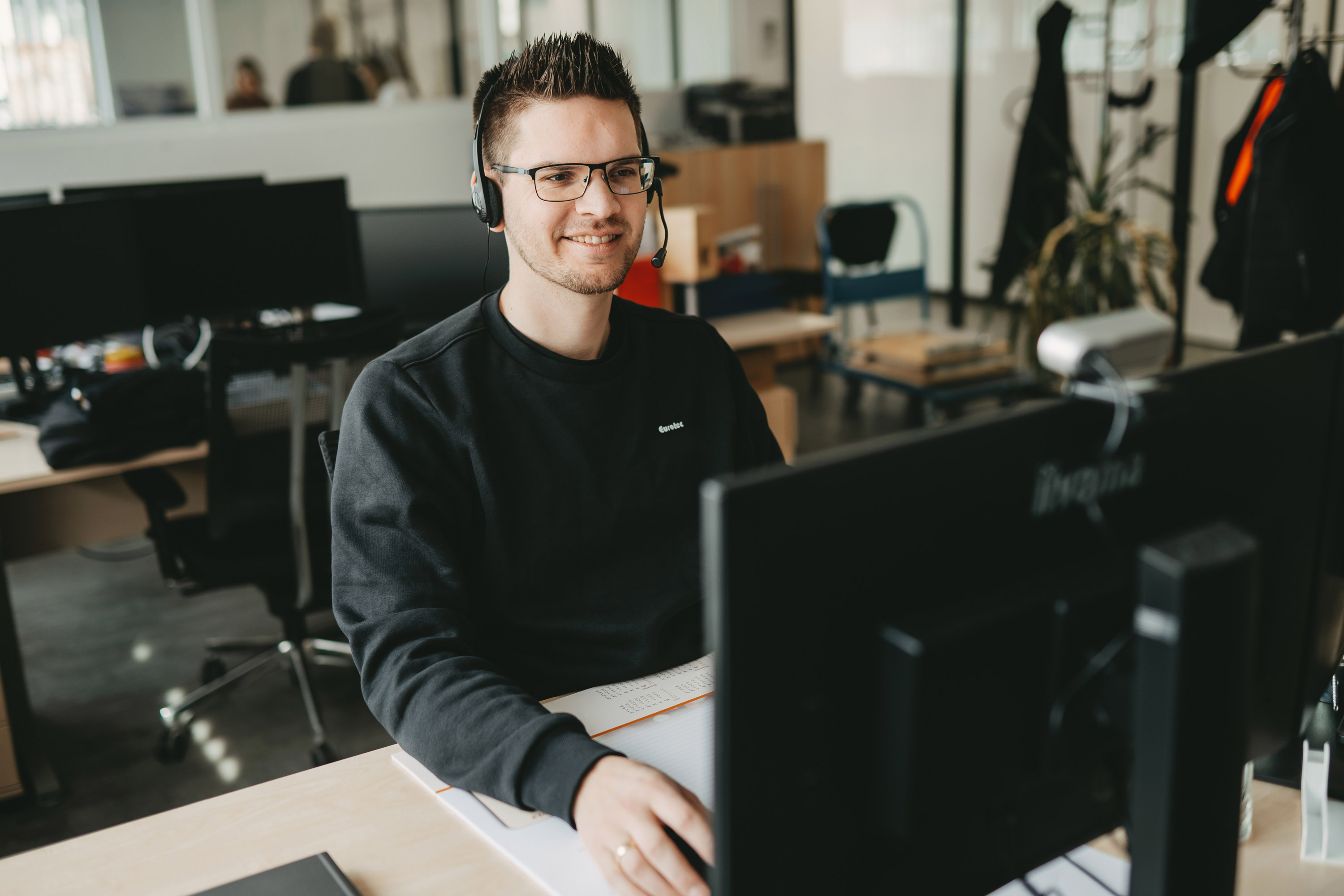
Nuestro Departamento de Tecnología y Construcción
¡Estaremos encantados de asesorarle en sus proyectos! Contacte con nuestro Departamento Técnico por e-mail en technik@eurotec.team, llámenos al +49 2331 62 45-444 o utilice nuestro software gratuito de planificación.
-
Novedades
¿Quiere estar siempre al día de las últimas novedades? En nuestra área de noticias encontrará una visión exclusiva de nuestra empresa. ¡Léala ahora!
más informaciones -
Catálogos
En nuestra zona de descargas encontrará todos nuestros catálogos y folletos para visualizar o descargar. Utilice la función de filtro para encontrar lo que busca rápida y fácilmente.
más informaciones -
Portal de empleo
¡En nuestro portal de empleo también tenemos el puesto perfecto para usted! Descubra qué vacantes tenemos y únase a nosotros para superarse a sí mismo. ¡Envíenos su CV hoy mismo!
más informaciones
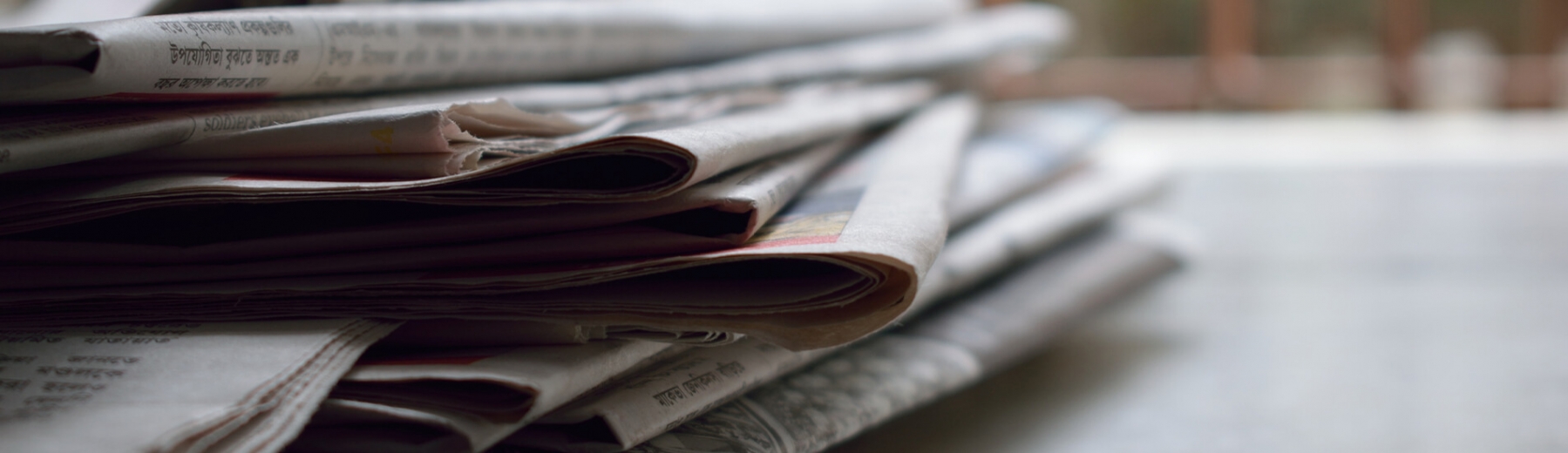