Производство
Наша продукция несет в себе разносторонние возможности применения — убедитесь в этом сами!
От поступающих в производство материалов до контроля качества — компания Eurotec делает ставку на инновационное производство с использованием новейших технологий, позволяющих удовлетворить самые высокие требования наших клиентов. Наша компания располагает 4 000 м2 производственных площадей, включая прилегающие зоны складирования и хранения.
Для производства полнонарезных саморезов мы используем наш универсальный станок, который охватывает все процессы от нарезания до отправки готовых саморезов на хранение.
фотоплёнка Eurotec
Технология штамповки и штамповки
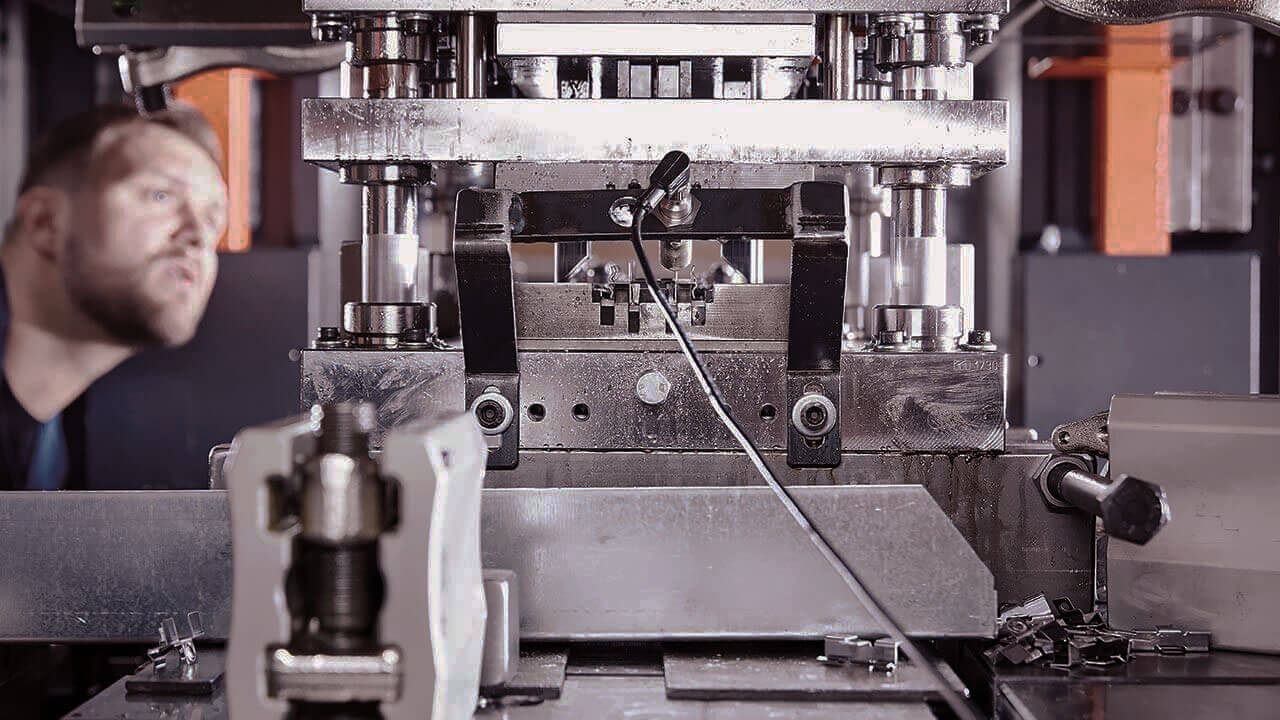
К одному из направлений нашей деятельности относится штамповка и гибка. Благодаря этим процессам мы создаем комплексные решения, которые используются нашими клиентами в самых разных областях по всему миру.
В нашем распоряжении находятся эксцентриковые прессы с усилием прессования от 40 до 400 тонн и максимальной скоростью 400 ходов в минуту. Это высокопроизводительное оборудование позволяет работать с лентой шириной до 500 мм и толщиной 0,15–8 мм. Производство осуществляется преимущественно из рулона с помощью специально разработанных инструментов для последующей нарезки или соединения. Посредством процессов штамповки и гибки изготавливаются зажимы для ромбовидного профиля, фасадные зажимы или уголковые соединители.
У вас возникли дополнительные вопросы? Наши специалисты будут рады проконсультировать вас по вопросам выбора материала и поверхности. Благодаря доступности различных конструкций и вариантов исполнения для каждой области применения может быть найдено оптимальное решение. Мы всегда находимся на связи со своими клиентами, что позволяет нам наилучшим образом удовлетворить все пожелания и требования.
Любые ваши требования будут удовлетворены одним производителем.
холодная штамповка
Eurotec полностью обеспечит вас необходимыми деталями!
С момента запуска производства в 2013 году мы постоянно расширяли наши мощности, и компания все больше наращивала объемы производства долговечных деталей, получаемых методом холодного формования на заводе в Хагене. К ним относятся, например, несколько видов монтажных шурупов, таких как наши полнонарезные саморезы ConstruX или кровельные саморезы Topduo. Наш парк, представленный современным оборудованием, позволяет осуществлять экономичное производство шурупов за один рабочий цикл. Таким образом, станки позволяют автоматизировать до восьми этапов обработки.
Сначала монтируется подводимый от катушек провод и нарезается до нужной длины. На наших производственных объектах изготавливаются детали холодного формования с диаметром до 16 мм и длиной до 3000 мм. Головка шурупа прессуется в два этапа: предварительный и окончательный. Затем формируется резьба. Предварительное фрезерование режущей кромки, тип 17, происходит непосредственно в процессе. Готовые шурупы упорядоченно складываются в транспортные контейнеры с использованием роботизированных систем.
Пластиковые шприцы
Также на нашем предприятии в Хагене мы применяем наш многолетний опыт работы в области литья пластмассовых деталей. Нами пройдена процедура сертификации системы менеджмента качества согласно ISO 9001. В нашей компании на регулярной основе проводятся проверки и контроль качества, что способствует повышению уровня удовлетворенности наших клиентов. Ассортимент производимой нами продукции включает в себя многомерные пластмассовые детали, изготовленные методом литья, такие как регулируемые опоры Profi-Line или различные адаптеры. Их особенными преимуществами являются устойчивость к атмосферным воздействиям и долговечность. В 2019 году мы произвели около 900 000 регулируемых опор и около 1 млн. зажимов для террас.
Благодаря современному оборудованию, включающему в себя во́семь станка для литья под давлением, мы можем обрабатывать широкий спектр термопластичных материалов в зависимости от потребностей и области применения.
Наши мощности рассчитаны на производство пластиковых деталей любых видов, применяемых в любой отрасли. Удерживающая сила наших станков находится в диапазоне от 30 до 220 тонн.
В связи с непрерывным расширением в начале 2018 г. весь наш станочный парк переместился в новый производственный цех.
технология экструзии
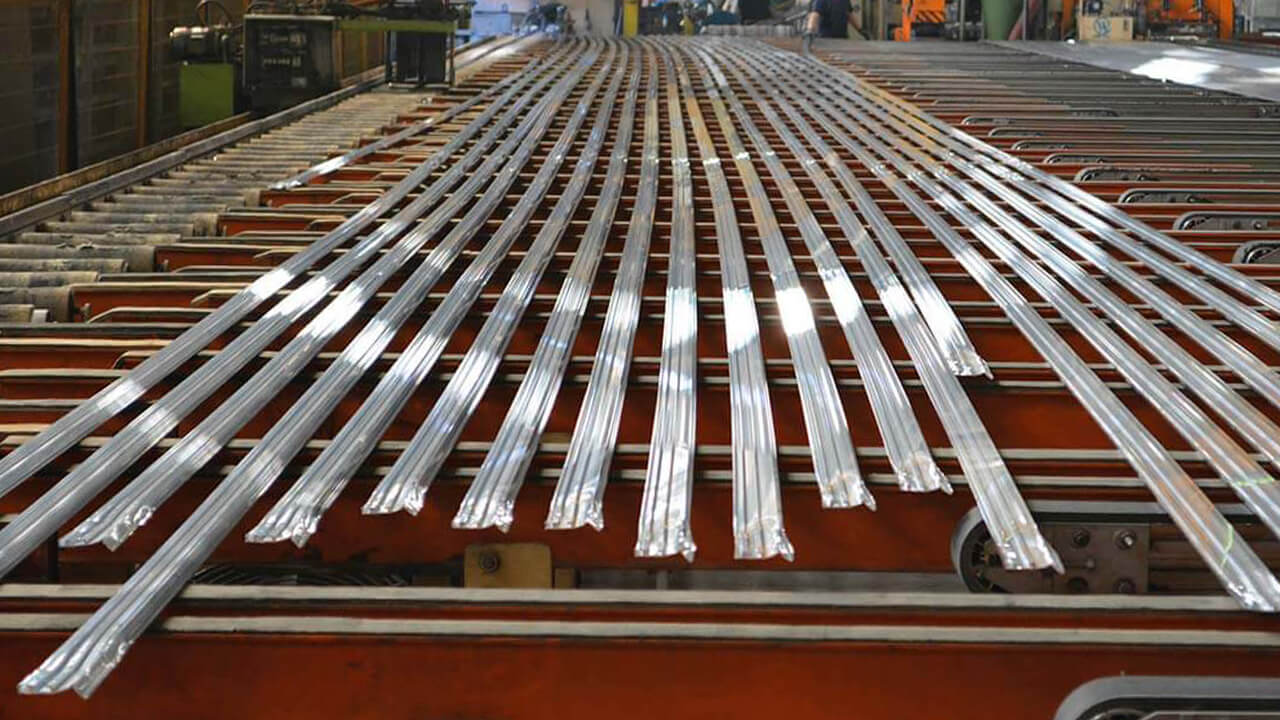
В ходе экструзионного процесса сырье нагревается и прессуется под давлением с помощью формовочного инструмента. Обычно для экструзии используется сплав EN AW 6063. В результате получают прямое прессованное изделие, которое обрезается в соответствии с необходимостью. С помощью экструзионной технологии производятся все алюминиевые системные профили, представленные в нашем ассортименте, такие как алюминиевый системный профиль EVO или Eveco. Этот процесс также используется при производстве террасной доски из ДПК.
Основным преимуществом является то, что очень сложные формы могут изготавливаться с высокой точностью и иметь при этом большую длину. Размеры варьируют в пределах от одного до шести метров.